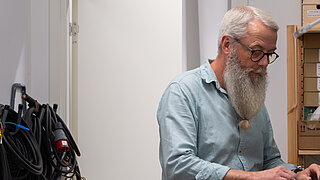
Motor Control: The Foundation of Unjo Technology Customized Solutions from a System Perspective
Selecting the most suitable motor for a specific application is a complex task that requires careful consideration of numerous critical factors as these elements can significantly impact overall performance.
Founded in the mid-1990s, Unjo Technology was established with the goal of enhancing electric motor performance through advanced motor control systems and a profound understanding of trajectory generation, interpolation, and synchronisation.
A meticulously designed control system can greatly improve the functionality of an individual motor, and this enhancement is even more pronounced in applications involving multiple motors and axes, where the demands on the control system are substantially increased.
Understanding the Overall System
When initiating a new project, it is essential to grasp the entirety of the system to optimize the interrelated subsystems. This includes not only the complete drive train but also adjacent systems that may influence or be influenced by the motor control solution. Focusing solely on the optimisation of individual subsystems can lead to suboptimal performance across the overall system.
Key Performance Needs
Unjo is committed to integrating motor controls with advanced functionalities to meet a wide range of performance requirements, including:
- A unified system capable of managing multiple motors
- Reduction in electricity consumption
- Enhanced performance metrics
- Minimized physical footprint and cabling
- Decreased noise and vibration levels
- Customized solutions tailored for battery-operated devices
Even if only one of these criteria is relevant to your application, collaborating with Unjo can yield substantial benefits. The complexity and demands of an application increase the likelihood that we can develop customized solutions based on state-of-the-art current, speed, and position control, combined with appropriate feedback to elevate your performance.
Unjo Core™: Expertise in Motor Control
With a large portfolio of successful development projects accumulated during more than 25 years, Unjo is expert at harmonising the optimal type and size of motor with bespoke control systems that deliver superior performance. Our expertise in DC and BLDC motor control, synchronous and asynchronous AC motor control and stepper motor systems allows us to offer:
- BLDC motor control for stable operation, high speed and low cost
- FOC (Field-Oriented Control), also know as vector control, for high accuracy and motor control bandwidth
- Over 30,000 stepper motor micro-step resolution
- Control of 1-16 axes on a single PCB
- One FPGA chip proven for 30+ axes
- Virtually unlimited signal processing capabilities, enabling fast response for high-speed dynamic motion and extraordinary low-speed properties
All of these features can be achieved simultaneously within a single system. By leveraging Field-Oriented Control (FOC) in our designs, we ensure optimal response across all performance parameters.
Motor and Transmission Optimisation
In addressing motor control challenges, we conduct a comprehensive analysis of the entire drive train to achieve genuine system optimisation. This evaluation considers essential factors such as torque, strength, smoothness, speed ranges, accuracy, component costs, and product durability.
Sensor Systems and Control Performance
Control performance is often dictated by the sensor system, which encompasses the capabilities of sensors and their signal processing. Customised solutions facilitate the integration of additional functionalities into the motor control unit, enhancing both compactness and cost-effectiveness. This may involve incorporating diverse measurements beyond traditional position, speed, and current sensors, including pressure, temperature, noise, humidity, and gas content.
Energy Efficiency
The Unjo Core™ expertise enhances energy efficiency, a critical factor in reducing life cycle costs and minimising energy resource consumption, particularly in battery-operated systems. By optimising the overall system and its operational conditions, we can lower component costs for OEMs and reduce energy consumption for end-users. Key strategies include:
- Intelligent motion adaptation
- Strategic selection and optimisation of motor types and sizes
- FOC (Field-Oriented Control) for maximum control and efficiency
- Closed-loop system design for improved efficiency
Application Examples
Case 1: DC Motor System
- Description: An ironless low-inertia DC motor combined with a miniature optical encoder and a high-quality zero-backlash gear, powered by a battery-operated control system with integrated Bluetooth radio.
- Result: Fast response with exceptionally smooth operation and high efficiency. The motion control exhibits responsiveness typically found only in high-performance direct-coupled systems, despite utilising a wireless remote control.
- Main Features: High-efficiency battery-powered application with integrated Bluetooth control, enabling excellent responsiveness and control of the mechanical system.
Case 2: BLDC Motor Control System
- Description: A multipole BLDC motor control system integrated with sensors and a belt transmission.
- Result: Transitioning from an asynchronous motor to a BLDC motor control yields unparalleled low-speed characteristics and a significant increase in efficiency. A redesigned transmission allows for an improved operating point, resulting in reduced weight and physical size, all while lowering system costs due to the low-cost motor with integrated feedback and high functional integration.
- Added Features: A compact, high-efficiency drive system that is modularized for scalability across different workload situations, providing a true low-cost customized solution with extended capabilities and ease of integration into various product versions and generations.
Case 3: Stepper/Multipole Motor System
- Description: A multipole permanent magnet hybrid stepper motor with current control, featuring unrivalled micro-step resolution through specially adapted field-oriented control.
- Result: Field-oriented control and very high current resolution enable smooth and precise stepper motor movements. With one motor turn divided into over one million steps, it can be positioned with extreme precision. Speed can be seamlessly increased to the motor's maximum speed, with the typical stepper motor noise nearly eliminated.
- Added Features: Extreme current resolution combined with groundbreaking frequency generation methods allow for smooth motor drive at high speeds without sacrificing low-speed precision.
Conclusion
Enhance your products’ performance with customized solutions from Unjo, a premier specialist in professional motor control systems. We design, develop, and produce customized solutions that optimize performance, offer lifetime support, and ensure rapid time-to-market. Discover how we can improve your product today with our expertise in Field-Oriented Control (FOC) and BLDC motor control and other advanced motor control solutions.